Behind the Charles Owen Badge: Helmet Materials
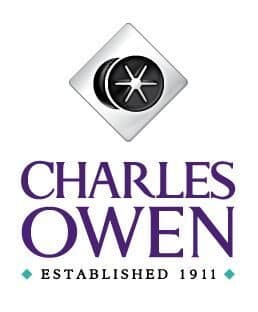
Helmets have come a long way from when they were being made out of cloth and shellac. Many of those advances are due to the plethora of modern materials. Selecting the right materials to be used in a Charles Owen helmet is an art in itself and is essential in creating the safest helmet possible.
The outermost layer of a Charles Owen helmet not only needs to be stylish but functional in preventing injury. A wide range of finishes exist from microfiber suedes, velvets, and leather looks to paints either textured or high gloss polyurethane. The fabrics are finished by stitching directly to the shell of the helmet - a step that distinguishes Charles Owen from many other helmet manufacturers. This allows Charles Owen to guarantee that the cover will never come away from the shell. Rubber-based glue is heat sensitive and fabric just glued to the shell can start to peel away, making stitching is the best way to ensure that long-lasting attachment.
The second layer of the helmet is the shell. Charles Owen makes the majority of its helmet shells out of fiberglass with a few more basic models from injection molded plastic. The new Charles Owen 4Star is made with aramid fibres embedded in a particularly tough resin matrix for vastly improved crush resistance. The purpose of the shell is to spread the force upon impact as well as keeping the integrity of the helmet when dragged along a rough surface. The shell is the key component in protecting the head against skull fracture should a horse tread or roll on you or when you fall on a sharp object such as a rock or corner of a cross-country post. It is the shell that provides protection from the concentrated impact of a stud, a protection that some safety standards do not require, but Charles Owen feels is important for its helmets. During the manufacturing process, the fiberglass shell resin cures for about four and half hours before the helmet goes on to the next step in the process.
Directly beneath the shell is the expanded polystyrene or EPS, the part of the helmet that absorbs the energy of the fall so that the brain does not bruise itself inside the skull. The polystyrene layer is made up of thousands of beads that are full of tiny air bubbles. The beads are foamed like popcorn and aged for about two weeks before the beads are welded edge to edge to create a continuous layer of expanded polystyrene. The absorption of energy by the polystyrene is the most important reason a helmet needs to be replaced after a fall - the impact bursts the contained air bubbles. If you were to fall on the same location again, the bubbles would not be there to absorb the energy of the fall. This part of the helmet has undergone the most evolution in recent years. Other sports with less energy of impact, but with a need to totally recover, have used materials such as memory foam, air chambers and deformable cones. Although not currently suitable for our level of performance, Charles Owen is always researching and testing these new technologies.
Inside the expanded polystyrene is the inner liner, which includes the comfort padding and sizing foam. This liner is made of fabric and foam that molds to your head over time and creates a comfortable and well-fitting helmet. This is the area with the most precision engineering, as the difference in a helmet size is only 1/16th inch in thickness. The helmet needs to interface efficiently with the skull and its inbuilt safety features and this is what differentiates helmet brands. The heads used in test labs are made from magnesium metal with no hair, skin or feeling. It is difficult to make a good helmet great without a full understanding the biomechanics, anthropology and ergonomics of heads.
The final part of the helmet is the harness system and its patented technology. Charles Owen uses reinforced nylon with a soft woven edge, soft leathers and suedes for the harness with either a quick release buckle or a hook and loop closure system. The harness is one of the most crucial components of the helmet because if the helmet doesn't stay on the head it cannot protect it. The harness is designed with precision to keep buckles away from the jawbone, reduce slippage and cup the base of the skull for maximum stability. With the variety of head shapes, not one harness style gives the best comfort with security and you will be amazed at how different each can feel.
All the key components used to create Charles Owen helmets are manufactured in the factory in Wrexham, United Kingdom. The helmets are assembled from start to finish by highly skilled helmet technicians. Using a cellular manufacturing process rather than a production line ensures quality, pride of workmanship and unparalleled traceability. From creating the first bubbles of polystyrene to placing the helmet in the distinctive purple box, the process takes about three weeks.
Now that the materials and manufacturing process has been explained, tune in next time for a look inside the quality control and safety testing that each Charles Owen helmet endures.